Cylindrical, full displacement piles enable faster and more efficient foundation construction.
Olivier in Rumbeke is no stranger to innovation. Founded by Gerdi Vankeirsbilck and now led by his son Dimitry, the company made waves in the foundation industry with the introduction of the now legendary Olivier full displacement screw pile in 1996. In 2017, it obtained a global patent for the screw pile without a lost drill tip, featuring a unique flaps system. More recently, it launched a new, cylindrical full displacement pile, which can be drilled into the ground even more easily, along with an automatic coupling for drilling pipes. These innovations quickly found their way to foundation companies worldwide.
Cylindrical piles for hard and/or unstable soil layers
The new cylindrical full displacement pile (Olivier DPA) allows construction on both less load-bearing and hard soil layers. The pile can be drilled without vibrations, even through layers of sand. In the case of large pipe diameters, the auger head is shorter than traditional FPD auger heads, resulting in less friction and significantly lower required drilling torque. This enables faster and more efficient work with considerably less fuel consumption during drilling. Additionally, the new system has the added advantage of eliminating the need for grout injection in hard sand layers. With smaller pile diameters, such as 360 mm, larger reinforcement cages can be placed through the drilling pipe. This is made possible by using a feed pipe with a diameter of 324 mm along its entire length. Numerous comparative tests with existing traditional systems have sufficiently demonstrated the speed and efficiency of Olivier’s new cylindrical pile system.
Unique flaps system with reusable drill tip
Thanks to the unique flaps system, the drill tip is no longer lost and can be reused each time. The drill tips no longer need to be manually placed, reducing the risk of accidents and injuries significantly. Furthermore, the reusable drill tip results in significant cost savings and reduces the need for transportation to the construction site, leading to reduced emissions. This is especially important considering that in Belgium alone, over 150,000 drilled displacement piles are made annually.
The patented flaps also ensure more precise positioning of the auger head. Installing the reinforcement and pouring concrete becomes a breeze as a result.
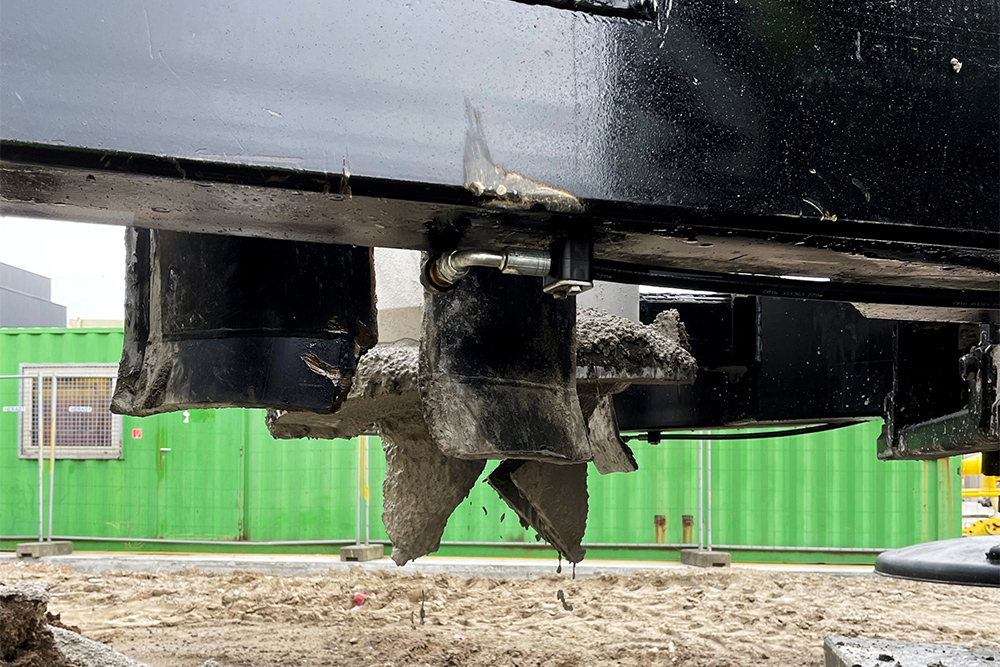
Automatic coupling for drilling pipes
A further innovation is the new patented automatic Olivier coupling, which is mounted under the rotary drive. This speeds up and ensures the safety of connecting the pipes to the machine, eliminating the need for anyone to climb to great heights to lock the coupling. In full displacement piling systems, the coupling can be used on pipes ranging from 133 to 914 mm.
The new coupling can also be used for closed concrete systems (e.g., with a double head rotary drive), allowing a full length reinforcement cage to be placed through the drilling pipe. After the drilling pipe is inserted into the ground, it can be disconnected in seconds, a reinforcement cage placed in the drilling pipe, and reconnected. The automatic coupling can transmit the maximum drilling torque clockwise and counterclockwise and is compatible with all existing Olivier couplings.
Logistics and Technical Support
Olivier offers customers tailored training for pile drilling, including on-site guidance for drilling teams at the construction site. In case of any issues, they are ready to provide on-site support. Production, maintenance, and repairs are carried out in their own workshop in Rumbeke, where other foundation accessories are also manufactured.